How Does Powder Coating Differ From E-Coating
Powder coating & e-coating are finishing procedures that provide a protective layer to the exterior of a material using electrical currents. Both methods provide a consistent, cured finish; however, that is where their similarities end.
Understanding the distinctions between these methods, as well as the benefits of each coating, is critical to selecting the optimal finish for your material. Find out how different coatings differ & which will best assist you to increase the lifespan of your material and give corrosion protection for your product.
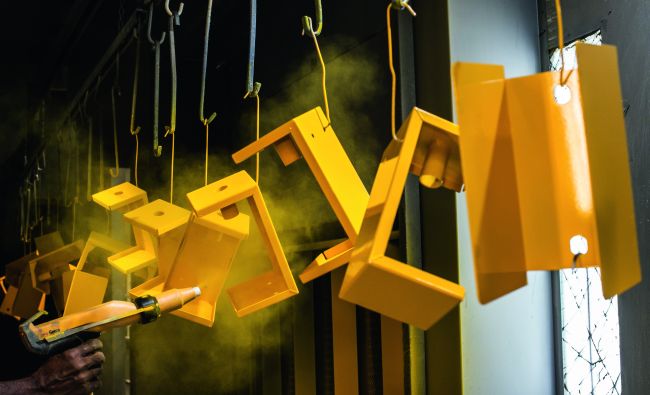
Powder Coating Vs. E-Coating
Although both powder coating & e-coating employ electric currents to bind particles to your material, the procedures are not the same.
Powder coating is a dry application procedure that uses a spray cannon to apply electrostatically charged paint powder to a grounded substrate. After finishing the spray coat, the technician places the material in an oven to melt the powder and create a uniform, cured surface.
Submerging your material in a water-based paint or epoxy solution is the e-coating technique, also known as electrophoretic deposition or electrocoating. Electrical currents are sent through the liquid, causing suspended particles to settle on the material's surface. When the technician is pleased with the thickness of the coating, the material is rinsed and transferred to a curing oven.
e-coat finishes are often applied to metal surfaces, although power coatings may be applied to a broader range of surfaces, such as metals, glass, wood, and some high-temperature plastics.
Advantages Of Powder Coating Over Other Processes
The powder coating should be used by outdoor furniture makers and suppliers instead of liquid coating. This efficient technique not only improves the aesthetics of the finish but also makes it endure longer. Other reasons why powder coated garden furniture is superior to liquid painted garden furniture include:
This process is used to provide a tough finish that is more durable than liquid paints. First, determine if the material is covered with liquid or powder; to be sure, try to scratch the paint with your nails. If it goes, this means that liquid painting has been used. Otherwise, it's powder coating. As a result, it actually has a greater level of durability.
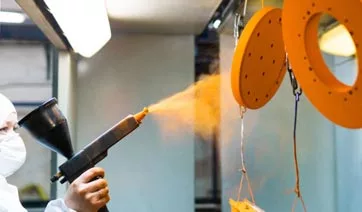
Powder layering gives a thicker finish than liquid paint when sprayed, and it does so without running or drooping. Liquid paint can droop and destroy the surface by forming lumps and layers, but powder paint produces far less visible changes.
When the powder from the gun is sprayed, it emits zero or near zero volatile chemicals (VOC). VOCs are organic compounds that are hazardous to human health, the environment, and everything that comes into contact with them.
Powder coating overspray may be recycled 100 percent, which means it does not pollute the environment with garbage. Now that you understand the differences between powder coating and other processes, you can make the best decision when purchasing items.
How Does The Powder Coating Process Work?
Pre Treatment
This is all about preparing the component or part, & preparation is critical in every painting job to produce the greatest possible result.
- It is necessary to remove oils, lubricants, and metal oxides, which is normally accomplished by a number of chemical and mechanical techniques, depending on the material, size, and finish desired.
- Chemical pre-treatments with many stages often entail the use of phosphates or chromates in submersion or spraying.
- Those supplying phosphate preparations are my preferred alternative from an environmental standpoint, as chromates may be hazardous to the environment.
- Sandblasting and shot-blasting are alternate methods of preparation in which blasting abrasives are employed to provide surface roughness and preparation for wood, plastic, or glass.
- Silicon carbide can be used to grind metals, and plastic media blasting uses plastic abrasives that are sensitive to substrates such as aluminum.
The Powder Application
- Electrostatic spraying with a spray cannon is the most common approach.
- The object is grounded, and the gun charges the powder with a positive electric charge, which is then sprayed and driven toward the component by the high electrostatic charge.
- When heated, the powder melts into a homogeneous layer, which is then chilled to produce a hard coating. We occasionally heat the metal first before spraying the powder over the heated substrate. Preheating can assist in obtaining a more uniform finish, but it can also cause other issues, such as powder runs.
- The powder can also be administered using electrostatic discs that have been specially designed.
- The Fluidised Bed process includes heating the substrate and then immersing it in an aerated, powder-filled bed.
- The powder bonds and melts to the heated item, necessitating additional heating to complete the curing coating. This approach is often utilized when the coating thickness reaches 300 microns.
- Electrostatic Fluidised Bed Coating: The same fluidizing processes as described above are used in electrostatic fluidized bed application but with significantly less powder depth in the bed. In the bed, electrostatic charging happens, and the powder becomes charged as the fluidizing air pulls it up. A cloud of charged powder particles forms above the fluid bed. When a grounded portion passes through a charged cloud, particles are drawn to its surface. The components have not been warmed.
- Electrostatic Magnetic Brush (EMB) coating is a finishing process for flat objects that uses powder coating with roller technique.
Curing
When thermoset powders are subjected to high-temperature rises (often through convection or infrared cure oven), they begin to melt, flow out, and then react to produce a greater molecular weight polymer. This curing process, known as cross-linking, necessitates a certain temperature for a specific period in order to achieve a full cure and develop the entire film qualities for which the material was intended.
Which Coating Is Perfectly Suited For Your Project?
The e-coating application procedure is especially well-suited for materials with numerous difficult-to-reach places since the submersion approach aids in coverage in those difficult-to-reach areas. E-coating also allows professionals to precisely regulate the thickness of the coating, resulting in ultra-thin surfaces that are extremely difficult to obtain with traditional methods.
Powder coating is generally the best solution if the primary aim of your finish is to protect your item from wear, weathering, & ultraviolet (UV) exposure. While e-coating has many of the same advantages, however, powder coating produces a thicker, more durable finish. Furthermore, since most e-coats are not UV stable, powder coating provides additional protection to objects that are exposed to the weather.
In most e-coating applications, the e-coat serves as a primer before a more protective, UV-resistant powder coating is applied. This combination is used in the automotive, appliance, & other industries where strong corrosion resistance is required. These components go through the e-coating process before being powder coated.